Why US Manufacturing Fails: Costs, Labor, Outsourcing
- Share
- Issue Time
- Apr 24,2025
Summary
Discover why US manufacturing struggles: high costs, labor shortages, outsourcing trends, and policy gaps hindering domestic production revival.
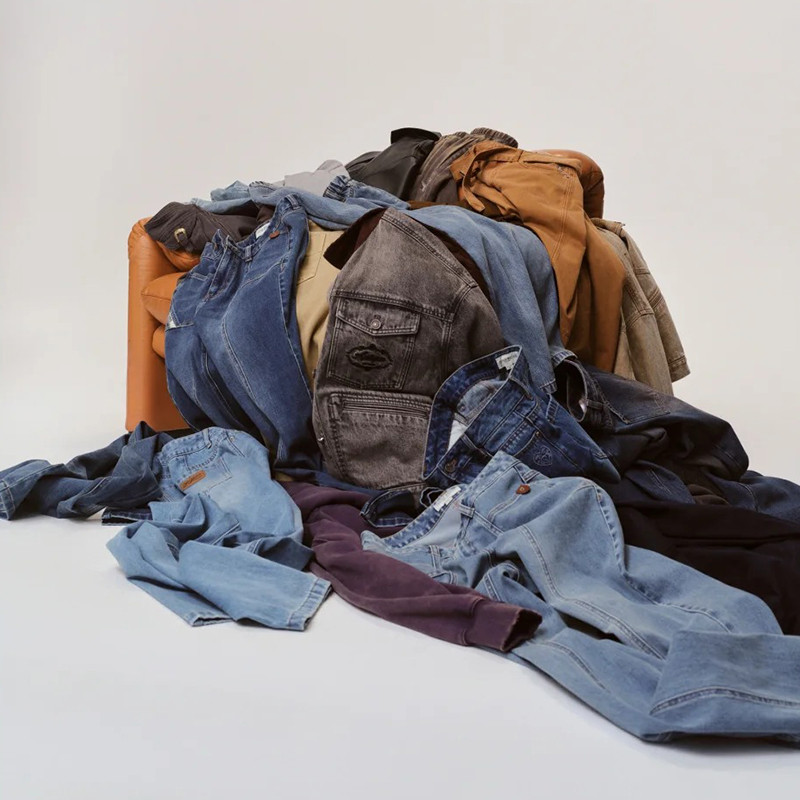
Why Can't We Start Manufacturing Goods in the USA?
Ever scroll through Instagram and see brands proudly shouting “Made in America,” yet wonder why so many factories still sit overseas? From eco-friendly denim to high-tech gadgets, companies dream of onshoring—but reality bites.
In a nutshell, America’s efforts to ramp up domestic manufacturing hit walls due to high wages, tangled regulations, gaps in infrastructure, and deep-seated reliance on global supply chains. Even with reshoring incentives, retooling factories and building skilled teams take years and hefty investment, making quick U.S. production surges tough to achieve.
1. What historical factors delayed U.S. industrialization compared to England?
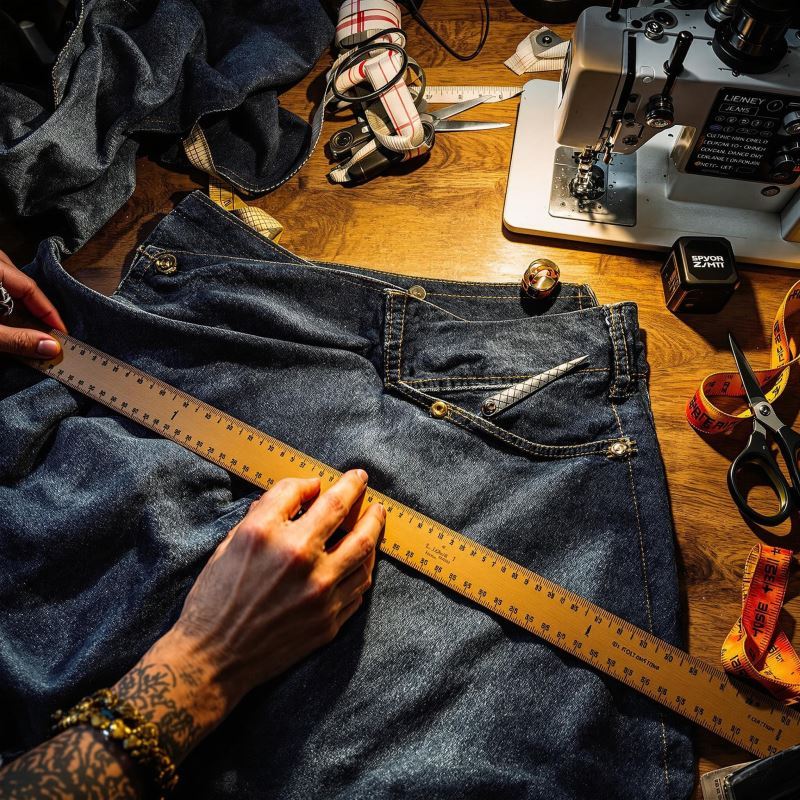
The vast farmland and emphasis on agriculture in the early United States, combined with the slow development of canals and railroads, conservative state-chartered banks, and a fragmented regulatory system after the Civil War, all hindered the development of factories.
The U.S. focused on agriculture, built transportation networks slowly, and lacked mature capital markets—while England’s textile mills, canals, and joint-stock financing fueled a head start.
Dive Deeper
①Resource focus on agriculture
·Vast farmland meant early American wealth was in tobacco, cotton, and grain—not factories.
·England’s soil constraints pushed it toward mechanized textile production as a primary growth engine.
②Transportation networks
·Canals & railways: England had 2,000+ miles of canals by 1800. The U.S. lagged behind until the Erie Canal (completed 1825) finally connected the Midwest to New York.
·Cost impact: Shipping a ton of coal 30 miles in 1800s New York cost $5; in Lancashire (England), the same was $1.50.
③Capital markets & investment
·Joint-stock companies in England raised millions of pounds to build mills.
·U.S. banks were state-chartered, conservative, and spread thin—entrepreneurs struggled to fund large-scale plants.
④Political-economic context
Fragmented regulations: Each U.S. state had its own rules, slowing expansion across borders.
Civil War aftermath: Devastated Southern infrastructure and diverted capital toward reconstruction, not new factorie
2. Why doesn't the U.S. manufacture certain goods domestically, and what does it not produce?
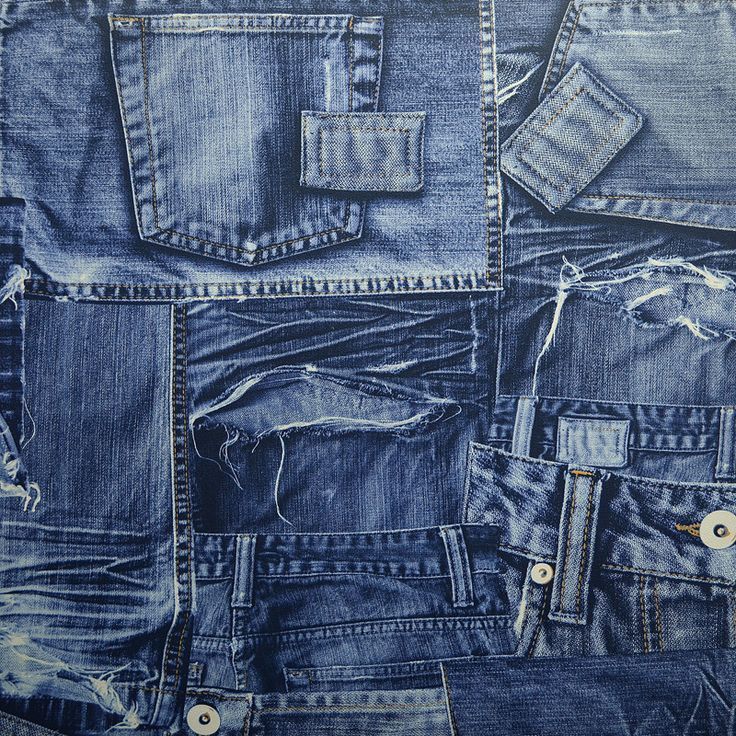
Due to high labor costs, limited rare earth mineral reserves and global supply chain optimization, approximately 97% of clothing in the United States is imported rather than produced domestically.
When countries have a clear edge—lower labor costs, unique minerals, or specialized skills—companies follow. The U.S. skips domestic runs for textiles, rare earths, and some electronics, importing roughly 97% of its apparel and key components.
Dive Deeper
①Comparative advantage
·Labor cost gap: Average garment-worker wage in Vietnam is $300/month vs. $3,000/month in the U.S.
·Volume play: High-volume assembly lines in Asia squeeze out smaller domestic runs on cost-per-unit.
②Location-specific resources
·Rare earths: China supplies ~80% of global rare earth minerals. U.S. deposits exist, but extraction is slow and regulated.
·Oil & gas: Gulf Coast refineries export petrochemicals cheaply; building new U.S. chemical plants is capital-intensive.
③Strategic supply-chain design
·Modular production: Brands might cut denim in Los Angeles, dye in Italy, and sew in Bangladesh—optimizing each step.
·Risk diversification: A single earthquake in Taiwan can’t halt your entire electronics line if parts come from multiple countries.
Examples
Category | % Imported by Value | Top Sources |
Apparel & Textiles | 97% | China, Vietnam, Mexico |
Electronics Components | 85% | South Korea, China |
Rare Earth Minerals (key) | 100% (net import) | China, Australia |
Pharmaceuticals (APIs) | 90% | India, China |
3. How important is manufacturing to the U.S. economy today, and what key facts illustrate its role?
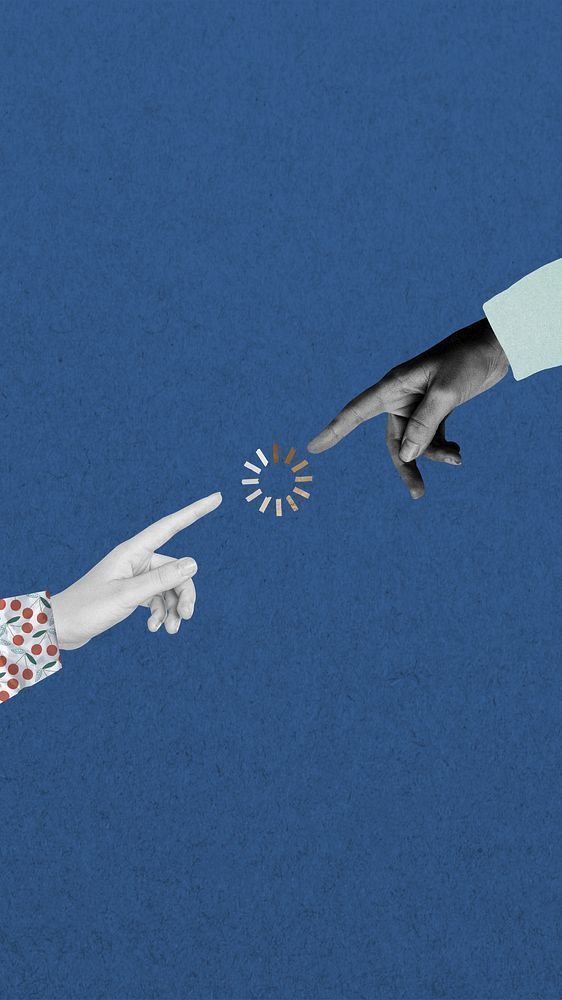
Manufacturing still accounts for about 11% of U.S. GDP, directly employs 11.5 million Americans, and generates $1.4 trillion in exports each year, making it an important engine of innovation and economic growth.
Dive Deeper
①GDP contribution
·1970s vs. today: Manufacturing fell from ~15% of GDP in 1970 to ~11% in 2023—but remains a productivity engine.
②Employment impact
·Jobs ripple: Every manufacturing role supports ~1.6 additional service and logistics positions.
·Core numbers: 11.5 million direct jobs; 19 million total when including supply-chain and R&D.
③Export earnings
·Top sectors: Aerospace ($160 billion), machinery ($140 billion), chemicals ($120 billion).
·Global reach: U.S. factories ship products to over 200 markets.
④Innovation spillovers
·Factory R&D: Companies reinvest ~5.5% of manufacturing revenues into research—double the average service sector.
·Tech transfer: Automated lines and IoT sensors often debut in car and aerospace plants, then trickle down to consumer goods.
Year | % of GDP | Direct Employment (M) | Exports (USD T) |
2010 | 12.1% | 12.5 | 1.2 |
2015 | 11.6% | 12.3 | 1.3 |
2020 | 11.0% | 12.0 | 1.35 |
2023 | 10.5% | 11.8 | 1.4 |
4. Which current barriers prevent scaling up manufacturing goods in the USA?
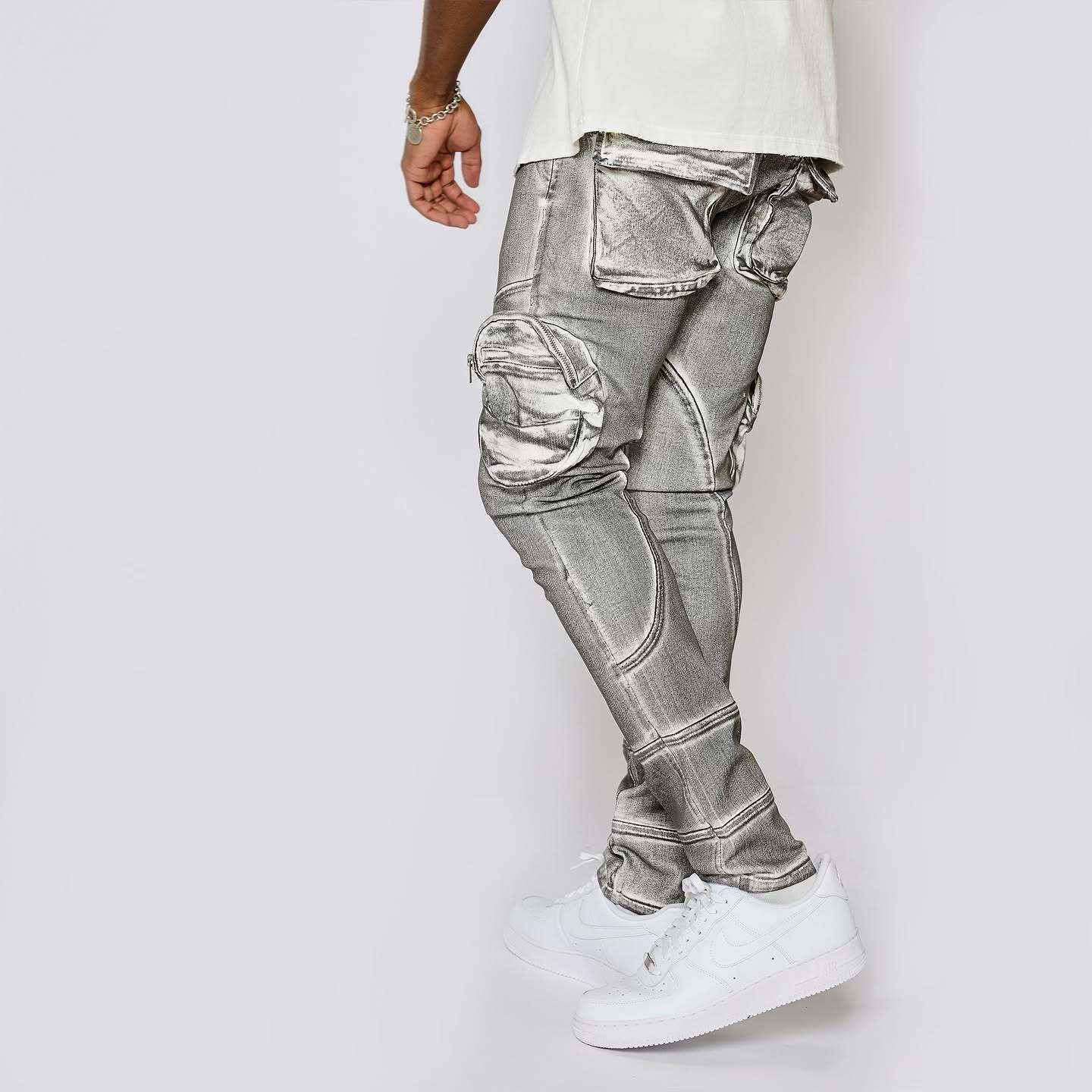
Sky-high labor costs, tangled regulations, massive capital needs, and global-tied supply chains make quick domestic scale-up a steep climb.
Dive Deeper
①Labor costs & skill gaps
·Wage comparison: U.S. factory workers average $23/hour vs. $4/hour in Mexico.
·Training crunch: Only 20% of U.S. high-school graduates pursue technical trades, creating shortages in CNC operators and welders.
②Capital-intensive build-out
·Plant cost: A mid-sized denim factory runs $10–20 million in equipment alone.
·Financing hurdles: Small brands struggle to secure loans without proven track records or collateral.
③Regulatory complexity
·Permitting timeline: Environmental and zoning approvals can take 18–24 months.
·Compliance costs: Installing wastewater treatment or VOC controls may add $2–3 million to startup budgets.
④Supply-chain fragmentation
·Component imports: Over 60% of critical inputs for a U.S. factory (zippers, dyes, specialty fabrics) remain offshore.
·Lead-time risk: Port strikes or freight-rate spikes can delay production by weeks.
⑤Raw materials access
·Domestic cotton: Covers only ~15% of U.S. fabric needs—rest comes from India and West Africa.
·Synthetic fibers: Most nylon and polyester resins are imported from Gulf Coast refineries.
Barrier | Impact | Estimated Cost/Delay |
Labor cost gap | +200–300% unit wage cost vs. offshore | $5–10/unit |
Permitting & compliance | 18–24 months before production | $2–3 million |
Capital equipment | High upfront CAPEX | $10–20 million per plant |
Component import dependency | Vulnerable to international disruptions | 2–4 week lead-time spikes |
Skill shortages | Limits capacity expansion | 20–30% unfilled skilled roles |
5. How do trade policies, globalization, and tariffs affect U.S. reshoring and production costs?
Dive Deeper
①Free Trade Agreements (FTAs)
·USMCA: Zero tariffs on auto parts crossing borders, boosting North American supply chains.
·18 FTAs: Covering 20+ countries, reducing duties on raw materials and finished components.
②Tariff uncertainties
·2018–2021 hikes: Steel and aluminum tariffs (up to 25%) and Chinese-goods surcharges (10–25%) injected cost volatility.
·Corporate hedging: Many shifted to multi-source strategies rather than full reshoring.
③Offshoring incentives
·Tax holidays: Some Southeast Asian countries offer 5–10 years of corporate tax breaks for new plants.
·Direct subsidies: Up to 15% of capex funded by local governments abroad.
④Reshoring case study
·Bain & Co. (2020): Only 12% of manufacturers reshored post-pandemic; 68% diversified suppliers instead.
·Budgeting headaches: Freight rates swung from $1,200 to $4,500 per container in 2021, making long-term cost forecasts tricky.
⑤Price volatility
·Currency swings: A 10% U.S. dollar appreciation can cut offshore production costs by roughly the same margin when converting back to dollars.
·Trade policy ping-pong: Shifting tariffs lead to “transit arbitrage”—routing through third countries to dodge duties.
Policy/Agreement | Key Benefit | U.S. Impact |
USMCA | Tariff-free auto parts movement | +4% regional auto production (2022 vs. 2017) |
KORUS | Zero duties on electronics inputs | Supported $50 billion annual trade volume |
China tariffs | 10–25% surcharge on $370 billion | +$50 billion in additional costs (2018–20) |
ASEAN FTA | Reduced duties on textiles & garments | Helped Vietnam apparel exports to U.S.+15% |
6. Are infrastructure, supply-chain, and environmental (climate change) challenges hindering U.S. manufacturing growth?
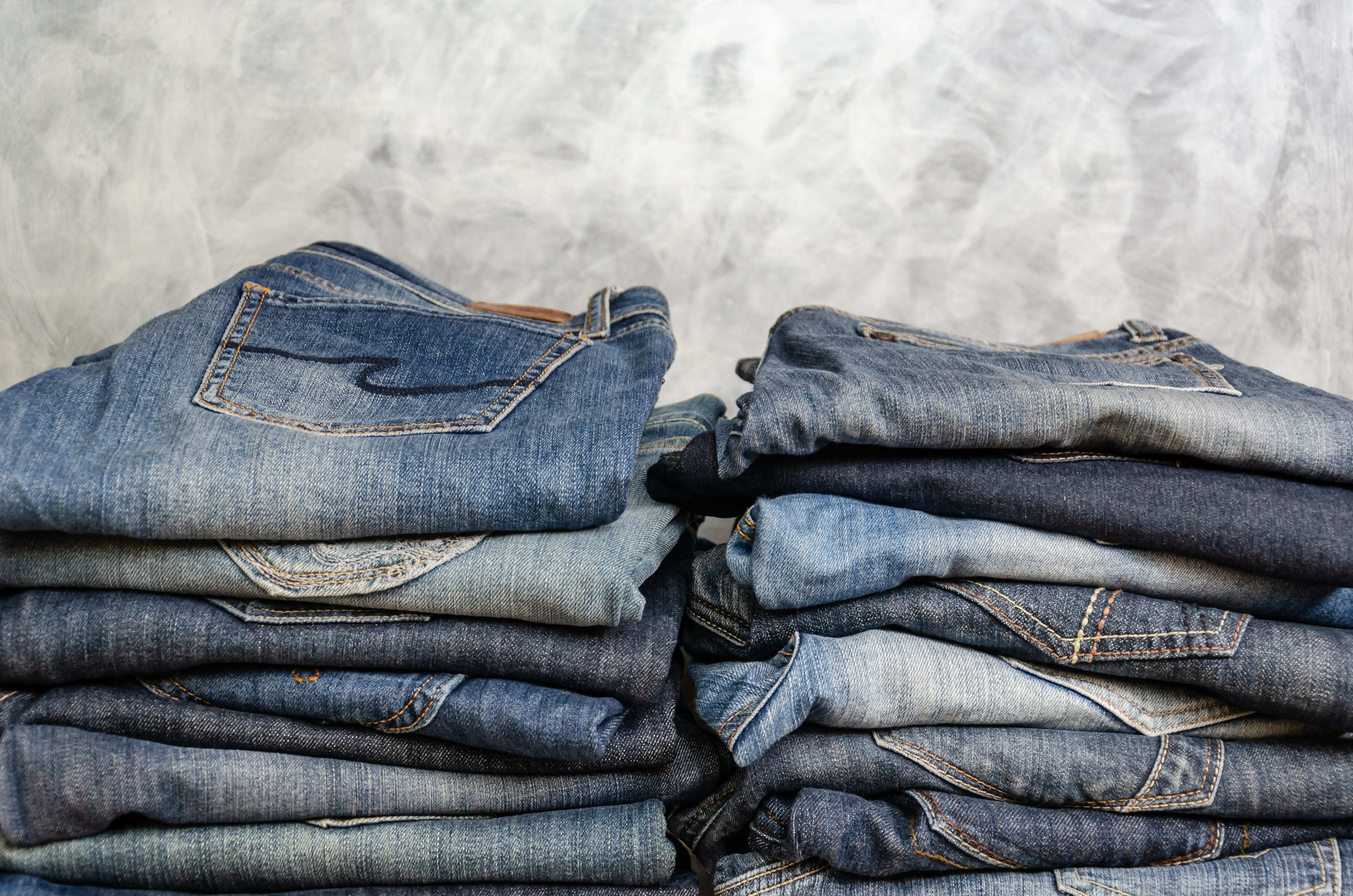
Aging ports and roads, logistics bottlenecks, and stringent environmental rules add hidden costs that slow expansion—and push companies to greener, offshore facilities.
Dive Deeper
①Aging ports & roads
·Infrastructure grades: 60% of U.S. highways are over 20 years old; nearly half of bridges need repair.
·Congestion costs: Port of Los Angeles waits average 5 days—sometimes up to 10 days during peak season.
②Logistics bottlenecks
·Trucking shortage: 80,000+ unfilled CDL jobs in 2023, driving freight rates 20% higher year-over-year.
·Rail delays: Grain and bulk shipments can be sidelined for weeks if chokepoints arise.
③Environmental compliance
·Water discharge permits: Textile plants face strict EPA limits on BOD and TSS, requiring expensive treatment.
·VOC regulations: Dye and finishing operations must capture or replace solvents, adding $1–2 million in CAPEX.
④Water usage & carbon footprint
·Denim wash: Traditional wash uses ~40 liters of water per pair. New closed-loop systems cut that by 85%.
·Energy intensity: Textile finishing can emit 2 kg CO₂ per kg of fabric—domestic power mix may be cleaner than coal-powered plants abroad, but compliance tech still costs up front.
At DiZNEW, we installed a zero-discharge wash line:
·Water saved: 85% reduction per batch
·Energy cut: 30% less electricity use
·Payback: Under 3 years thanks to water and utility rebates
7. Is manufacturing a viable business in the USA, and how can automation, advanced technologies, and new business models revitalize domestic production?
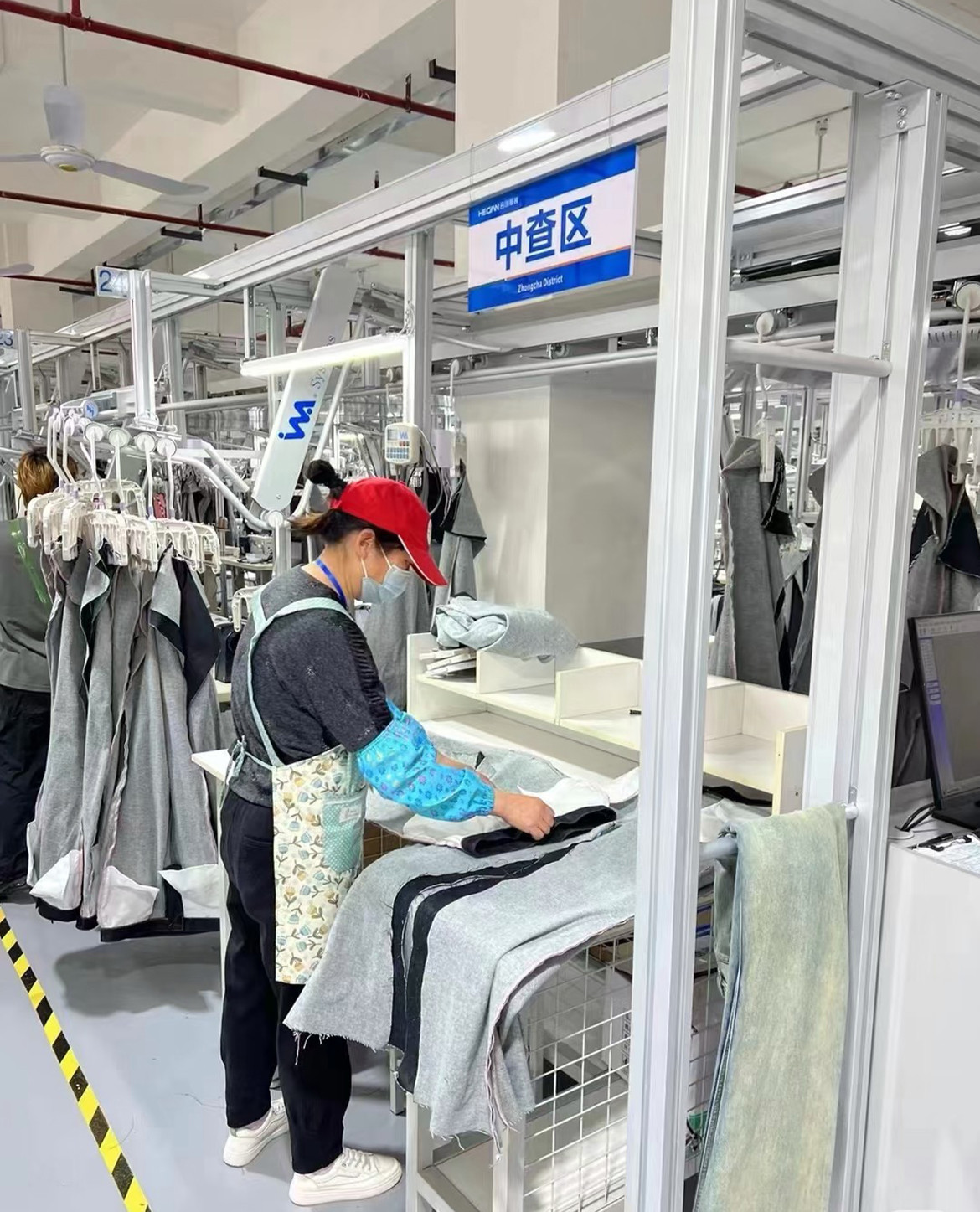
By embracing automation, Industry 4.0, and small-batch OEM/ODM models, U.S. factories can compete—offering speed, customization, and sustainability to premium brands.
Dive Deeper
①Automation & robotics
·Cobots: Collaborative robots handle repetitive cuts and seams, reducing labor needs by up to 40%.
·ROI: Typical cobot installation costs $50–80k, with payback in 12–18 months on labor savings.
②Industry 4.0 integration
·IoT sensors: Real-time monitoring flags machine wear before breakdown—lifting overall equipment efficiency (OEE) from ~65% to ~85%.
·Predictive maintenance: Cuts unplanned downtime by 30–50%, crucial for tight lead-time runs.
③Flexible OEM/ODM models
·No capex for clients: Brands pay per unit; factories invest in equipment.
·Low MOQs: Start at 30 pieces, letting you test designs and demand before committing to larger orders.
④Customization & small-batch focus
·Direct-to-consumer advantage: Limited editions drive hype and allow 2–3× price premiums.
·Digital sampling: 3D design tools eliminate physical prototypes, slashing sample times from 4 weeks to under 1 week.
DiZNEW success story
Metric | Offshore Partner | DiZNEW (USA) |
MOQ | 500 pieces | 30 pieces |
Lead time (sample to final) | 8–12 weeks | 4–6 weeks |
Quality revision rate | 15% | 5% |
Sustainability compliance cost | $1.5 million | Covered by rebates |
1.Will manufacturing ever come back to America?
While a full-scale return to 20th-century manufacturing is unlikely, rising reshoring trends fueled by automation, supply chain resilience demands, and government incentives like the CHIPS Act are driving a advanced manufacturing revival – particularly in semiconductors, EVs, and aerospace – creating 800,000+ new U.S. factory jobs since 2020 according to DOL data."
2.Why are things not made in America?
While decades of offshoring for lower labor costs and relaxed regulations shifted production abroad, 2023 Reshoring Initiative data shows record U.S. manufacturing rebounds in batteries, renewables, and medical gear, driven by automation, supply chain risks, and policies like the Inflation Reduction Act's $52B domestic production incentives.
3.Why did U.S. manufacturing go overseas?
U.S. manufacturing moved overseas primarily due to lower overseas labor costs, globalization incentives like NAFTA (1994) and China's WTO entry (2001), and corporate supply chain optimization – though 2023 Reshoring Initiative reports show 16% year-over-year growth in returning production, driven by automation and $500B+ in new federal investments for domestic semiconductor and clean energy manufacturing.
4.Why did the USA deindustrialized?
The USA deindustrialized due to globalization-driven offshoring of manufacturing, automation reducing labor demand, rising production costs compared to emerging markets, trade policy shifts like NAFTA, and strategic pivots toward service-based and technology sectors – key factors often explored in economic analyses of post-industrial transition.
Conclusion
At DiZNEW—a China-based OEM/ODM expert—we've cracked the code: delivering custom denim in as few as 30 pieces, with four-week lead times, top-tier quality, and up to 85% water savings. We bridge U.S. brands to world-class Chinese production prowess, offering turnkey, eco-smart manufacturing.