How Jeans Are Made: A Step-by-Step Guide
- Share
- Issue Time
- Mar 26,2025
Summary
Discover how jeans are made from start to finish with this easy-to-follow, step-by-step guide. Learn the secrets behind denim production!
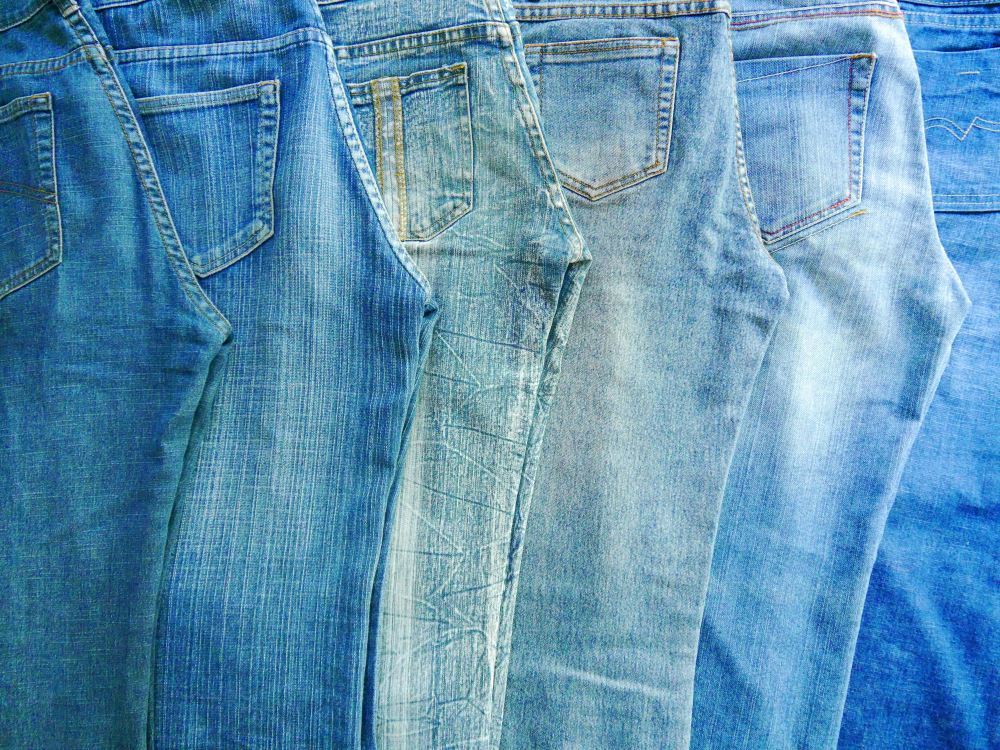
How Jeans Are Made: A Step-by-Step Guide
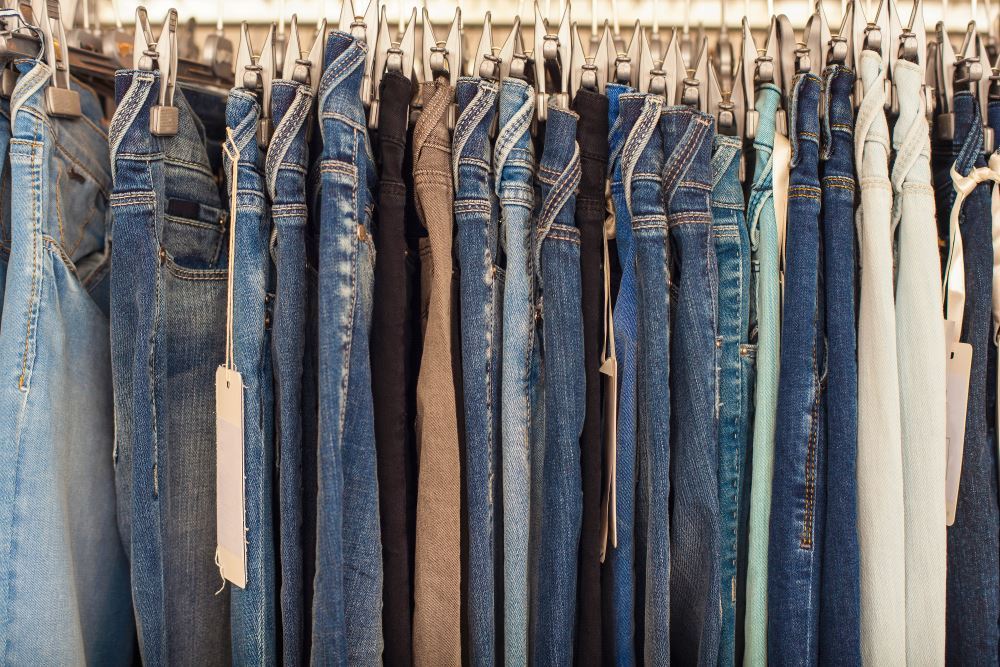
Jeans are more than just a wardrobe staple—they’re a testament to a rich heritage of craftsmanship and innovation. In today’s fast-paced world, understanding the production process of jeans can reveal insights into quality, sustainability, and style.
Featured Snippet:
Jeans are made through a systematic process that transforms raw cotton into durable denim. The journey involves material selection, fabric weaving, indigo dyeing, cutting, sewing, and finishing treatments to create the iconic blue jeans. Each stage ensures quality, style, and sustainability for diverse lifestyles.
Imagine walking through a buzzing factory floor, where modern machinery and skilled hands unite to craft each pair of jeans—a blend of technology and tradition that captures the essence of urban cool. Read on as we take you behind the scenes of jeans manufacturing.
1. What Are Jeans Made Of?
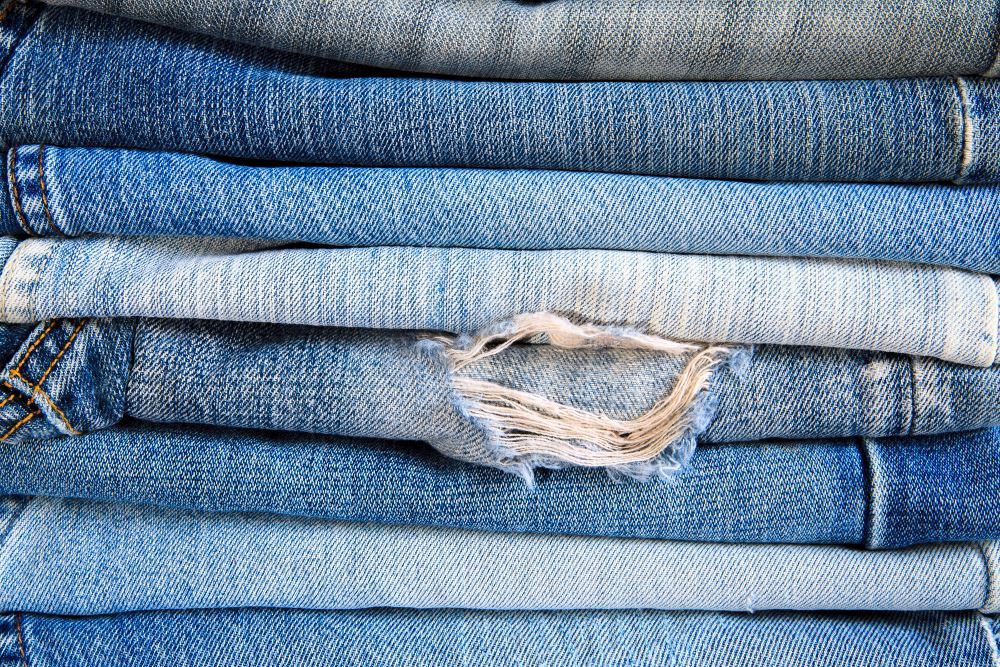
Quick Answer:
Jeans are primarily made of cotton, blended with small percentages of synthetic fibers for added strength and stretch. The denim fabric is woven in a twill pattern, with indigo dye providing the signature blue hue, ensuring durability and comfort.
Dive Deeper: Understanding the Materials
1.1 What Is Jeans Made Of?
Jeans begin with raw cotton, the natural fiber chosen for its softness and breathability. In many modern applications, cotton is blended with polyester or elastane to improve durability, flexibility, and resilience. These blends not only enhance the fabric’s performance, but also contribute to a comfortable fit.
1.2 What Is Jeans Made Out Of?
Beyond cotton, jeans can incorporate recycled fibers and innovative materials aimed at reducing environmental impact. Manufacturers are increasingly exploring organic cotton and recycled denim options. These alternatives support sustainable practices, while maintaining the classic look and feel of traditional denim.
1.3 How Jeans Fabric Is Made
The creation of denim fabric is an intricate process. After harvesting, cotton is cleaned, spun into yarn, and then woven in a twill pattern, which gives denim its distinctive diagonal ribbing. This weaving method contributes to the fabric's durability and resistance to wear.
1.4 Denim Fabric: What Makes It Unique?
Denim’s uniqueness lies in its weaving and dyeing methods. The warp (vertical threads) is often dyed with indigo, while the weft (horizontal threads) remains undyed. This results in the fabric’s characteristic faded appearance over time. A closer look reveals the craftsmanship behind the fabric's texture and resilience, making it ideal for both fashion and function.
2. How Is Denim Fabric Made?
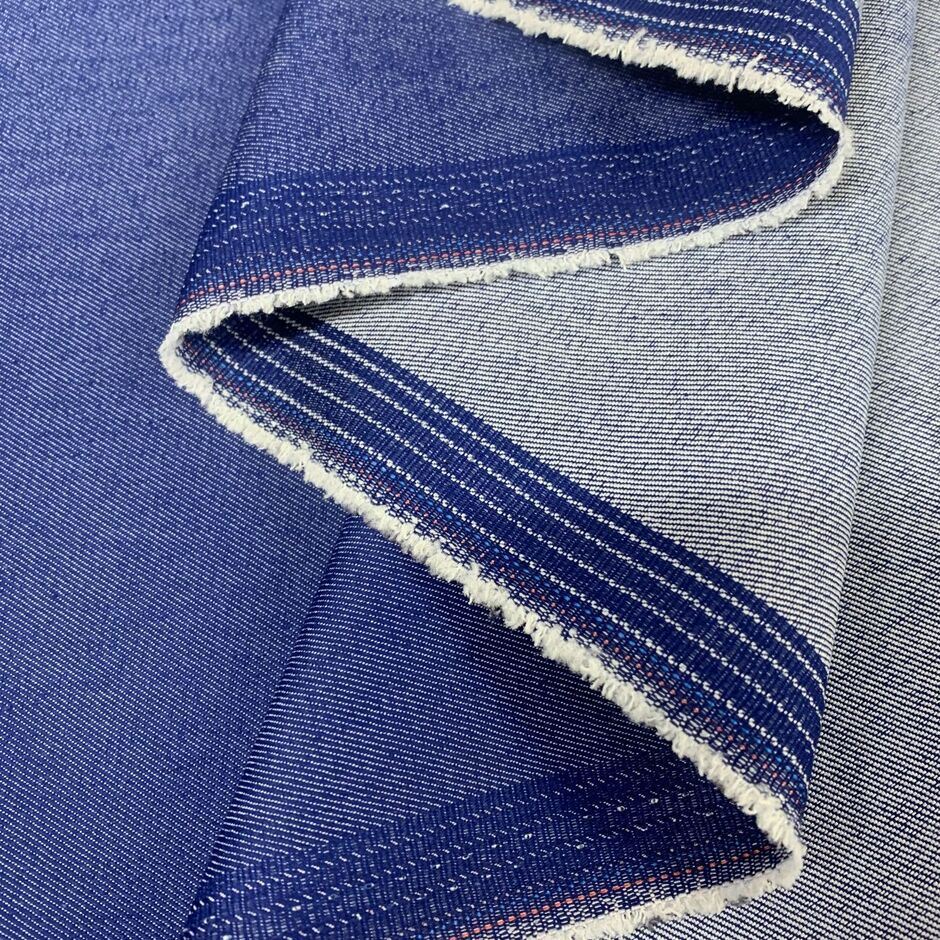
Quick Answer:
Denim fabric is made by spinning cotton into yarn, which is then dyed—usually with indigo—and woven in a twill pattern. The result is a robust, diagonal-textured fabric that forms the foundation of high-quality jeans.
Dive Deeper: The Fabric Creation Process
2.1 How Denim Is Made
The process begins with cotton selection, where quality fibers are chosen for spinning. After cleaning and carding, the cotton is spun into yarn. This yarn undergoes a dyeing process, typically with indigo, to achieve that iconic deep blue color. Finally, the yarn is woven in a twill pattern, giving the fabric its strength and distinctive look.
2.2 Why Are Jeans Blue? (Indigo Dyeing Process)
The blue hue of jeans is largely due to the indigo dye used in the process. Indigo dye has a unique characteristic—it does not fully penetrate the fibers. Instead, it adheres to the surface, allowing gradual fading that creates a worn, vintage appearance over time. This is why jeans become more characterful as they age.
2.3 How Are Blue Jeans Made?
Blue jeans are essentially crafted by repeating the steps of denim fabric creation with an extra emphasis on the indigo dyeing process. Modern techniques include using digital dyeing methods and water-saving technologies to ensure consistent color and reduced environmental impact. This integration of tradition with technology ensures the jeans not only look good but also meet high sustainability standards.
3. How Are Jeans Manufactured?

Quick Answer:
Jeans manufacturing involves converting denim fabric into a wearable product through cutting, sewing, and assembling. This process includes pattern making, fabric cutting, and stitching, followed by quality control to produce jeans that are both stylish and durable.
Dive Deeper: From Fabric to Finished Product
3.1 How Jeans Is Made
The transformation from denim fabric to jeans involves several steps. After the fabric is produced, it is inspected for consistency and defects. Patterns are then created based on design specifications. The fabric is laid out and cut using precision machinery to ensure minimal waste.
3.2 How Are Jeans Made?
Following cutting, the pieces are assembled through a series of sewing operations. Specialized machines sew pockets, waistbands, and decorative features, integrating both traditional techniques and automated technology. The focus is on accuracy and efficiency, ensuring every pair of jeans meets the desired specifications.
3.3 How Are Jeans Made Step by Step
A typical jeans production line includes:
Pattern Making: Designing templates for all denim pieces.
Cutting: Using computerized systems to accurately cut fabric.
Sewing: Assembling parts with industrial sewing machines.
Finishing: Washing, distressing, and quality-checking.
Packaging: Final inspection and packaging for shipping.
A detailed production flow table might look like this:
Stage | Process Description | Key Equipment | Time (hrs) |
Material Preparation | Cleaning, carding, and spinning cotton | Carding Machines | 4 hours |
Weaving | Woven in a twill pattern with indigo-dyed yarn | Industrial Looms | 6 hours |
Cutting | Pattern cutting with computer-guided systems | Cutting Machines | 3 hours |
Sewing | Assembling pieces into a pair of jeans | Industrial Sewing Machines | 5 hours |
Finishing | Washing, distressing, and final inspection | Washing Machines, Finishing Tools | 4 hours |
Packaging | Final packaging and quality check | Packaging Equipment | 2 hours |
3.4 How Are Levi’s Jeans Made?
Levi’s, the iconic denim brand, has refined the jeans-making process to near perfection. Their production includes proprietary treatments like specialized indigo formulations and unique stitching techniques. Levi’s also emphasizes stringent quality checks, with each pair undergoing multiple inspections to ensure durability and style. For example, Levi’s uses high-tensile rivets and branded hardware to enhance jeans longevity and brand identity.
3.5 How Pants Are Made: A Broader Context
While jeans are a specific style, the manufacturing process for most pants follows similar principles. Variations occur in fabric type, design complexity, and finishing techniques, which are tailored to the intended use—whether for casual wear, work, or high fashion. This broader context helps us appreciate the nuances of jeans production, highlighting why denim remains a preferred choice for durability and style.
4. How Are Jeans Cut, Sewn, and Assembled?
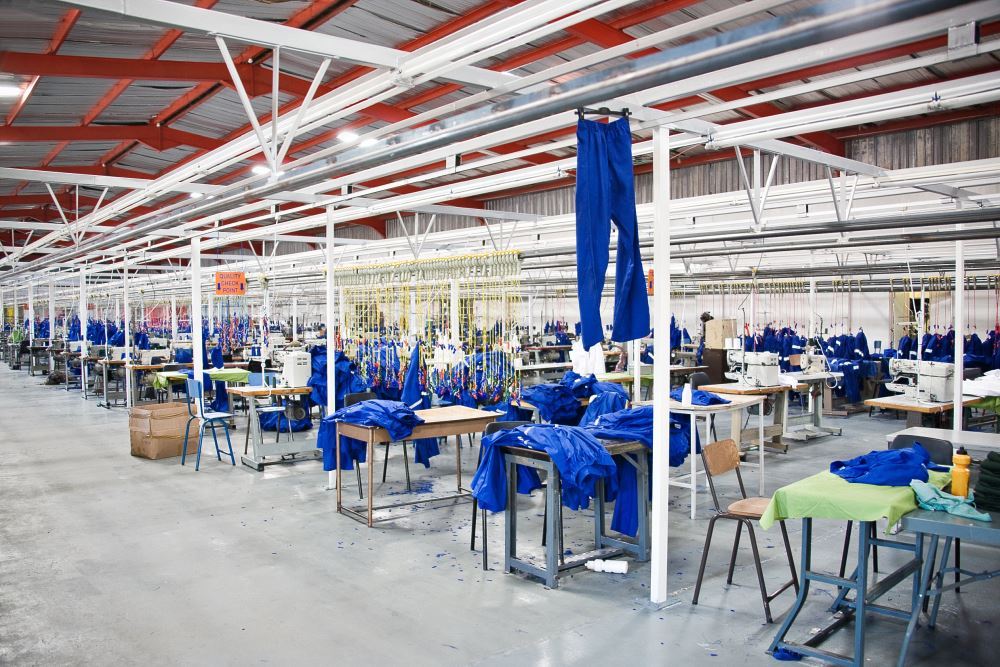
The assembly process of jeans is where precision meets creativity. This stage brings together the meticulously cut fabric pieces into a finished garment that combines both comfort and aesthetic appeal.
Quick Answer:
Jeans are cut, sewn, and assembled using precise patterns and advanced machinery. Skilled workers and modern technology ensure every component, from pockets to seams, is perfectly aligned and securely stitched.
Dive Deeper: The Assembly Line in Detail
4.1 The Cutting Process
Once the denim fabric is woven, it is spread out and laid flat in the cutting room. Here, digital templates and computer-guided cutting machines ensure that every piece of fabric is cut accurately. This precision is critical for both the fit and the overall look of the jeans. In many modern factories, automated cutting can reduce fabric waste by up to 15%, making the process more efficient and eco-friendly.
4.2 Sewing Techniques
After cutting, the fabric pieces move to the sewing section. The assembly process involves:
Stitching Methods:
Lockstitch: Offers strong, durable seams.
Chain Stitch: Provides flexibility in areas that require movement.
Decorative Stitching: Enhances the aesthetic appeal of the jeans.
Skilled operators constantly monitor the machines to adjust thread tension and ensure consistency. Workers are trained to recognize even minor defects that automated systems might miss, ensuring that every seam meets high-quality standards.
4.3 Assembly and Quality Assurance
After the sewing stage, all pieces are assembled into the final product. Quality control is integrated at every step. Each pair of jeans undergoes multiple inspections—from visual checks of the stitching to measurements ensuring a consistent fit. The final product must meet strict quality standards before it is approved for packaging and shipment.
Below is a quality checklist table that many manufacturers use:
Inspection Stage | Criteria | Tolerance | Inspection Method |
Pre-Production | Fabric quality & color uniformity | N/A | Visual and machine checks |
Cutting | Accuracy of pattern cuts | ±1-2 mm | Digital calipers |
Sewing | Stitch consistency & strength | Uniformity | Manual and automated checks |
Finishing | Washing and distressing uniformity | Consistent fade | Visual and sample testing |
Final Packaging | Overall appearance & measurements | ±0.5 inch in measurements | Final quality inspection |
5. How Are Jeans Treated and Finished?
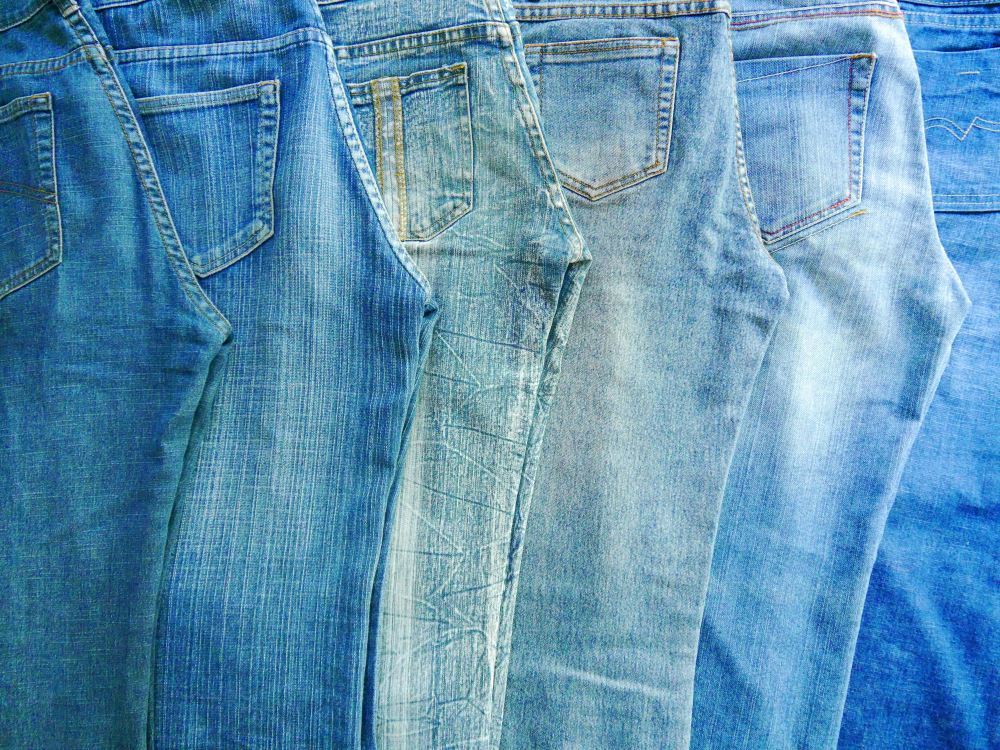
The finishing stage transforms a plain pair of jeans into a stylish and comfortable garment with a distinct personality. Finishing involves several treatments that enhance the look, but also the feel of the fabric.
Quick Answer:
Jeans undergo washing, distressing, and finishing treatments to soften the fabric, create unique wear patterns, and enhance visual appeal—all while ensuring durability and sustainability.
Dive Deeper: Finishing Touches on Denim
5.1 Washing and Distressing Techniques
Finishing often starts with washing, which can include various methods:
Stone Washing: Using pumice stones to create a worn, soft finish.
Enzyme Washing: Using natural enzymes to break down fibers, producing a gentle fade.
Acid Washing: Creating a more dramatic, faded look through chemical treatments.
These processes not only soften the denim, but also help achieve that “lived-in” look that many consumers love. For instance, some brands report that enzyme washing can reduce production time by 20% compared to traditional methods.
5.2 Modern Finishing Technologies
In recent years, innovations such as ozone washing and laser distressing have revolutionized the finishing process. Ozone washing can cut water usage by up to 50%, while laser technology allows precise distress without physical abrasion. These methods contribute to environmental sustainability and consistent quality.
5.3 Styling and Custom Finishing
Customization is a growing trend in the denim industry. From embroidery to unique patches and even digital printing, brands are finding creative ways to differentiate their products. Consider this example: a survey of 500 consumers found that 65% prefer jeans with subtle distressing, and 35% enjoy bold, custom embellishments. This data is driving more factories to offer personalized finishing options.
A sample custom finishing options table might look like this:
Finishing Option | Description | Popularity (%) | Production Time Impact |
Enzyme Wash | Softens fabric with a natural fade | 65 | -10% faster |
Stone Wash | Uses pumice stones for a rugged look | 50 | Standard |
Laser Distressing | Precision distressing with lasers | 40 | +5% production time |
Embroidery/Patches | Custom designs for personalization | 30 | Varies |
6. How Are Jeans Measured and Quality-Controlled?
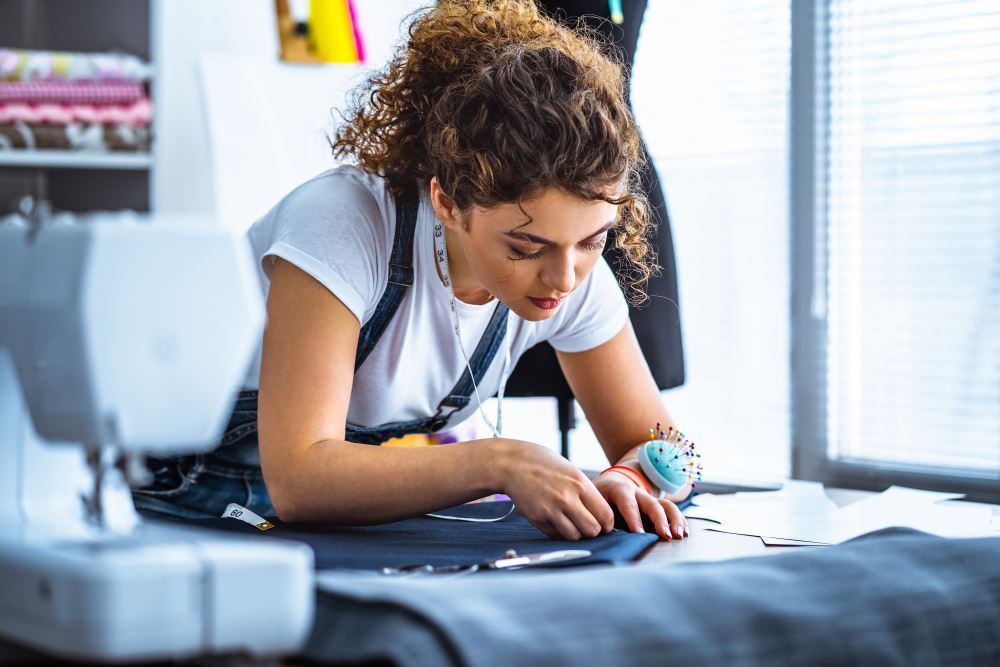
A key element in jeans manufacturing is ensuring that every pair fits perfectly and meets rigorous quality standards. This involves precise measurements and continuous quality checks throughout the production process.
Quick Answer:
Jeans measurement is achieved through digital templates and manual checks, ensuring consistency in size and fit. Quality control is integrated at each stage—from raw materials to the final product—to guarantee durability and comfort.
Dive Deeper: Ensuring the Perfect Fit
6.1 How Are Jeans Measured?
Measurement begins in the design phase, where patterns are meticulously drafted to cover all sizing requirements. Key dimensions include:
Waist: Typically measured with a tolerance of ±0.5 inches.
Inseam: Consistency is key for leg length.
Rise and Leg Width: Critical for ensuring overall fit.
Many factories now employ automated systems alongside manual checks to ensure that each pair of jeans adheres to standard sizing charts. For instance, a digital measurement system can reduce sizing errors by over 90% compared to manual measurements alone.
6.2 Quality Control Methods
Quality control is a continuous process:
Pre-Production: Raw materials are inspected for consistency in color and texture.
In-Process Checks: During cutting and sewing, automated systems and quality inspectors verify each piece.
Final Inspection: Before packaging, each pair undergoes a thorough check against a standardized checklist.
The following table illustrates a simplified quality control process:
Quality Stage | Checkpoints | Tools Used | Tolerance Level |
Raw Materials | Fabric color, texture, fiber quality | Visual inspection, sample tests | High quality only |
Cutting | Pattern accuracy, waste minimization | Computerized calipers | ±1-2 mm |
Sewing | Stitch consistency, seam strength | Manual review, tensile testers | Uniform stitches |
Final Product | Fit, overall appearance, durability | Digital measurement tools, visual review | ±0.5 inch variance |
6.3 Incorporating Customer Feedback
In today’s market, customer feedback plays a crucial role in refining production. Many manufacturers use surveys, social media insights, and direct feedback to adjust designs and improve fit. This iterative approach ensures that each new production batch is better aligned with consumer preferences.
7. How to Get Jeans Manufactured?
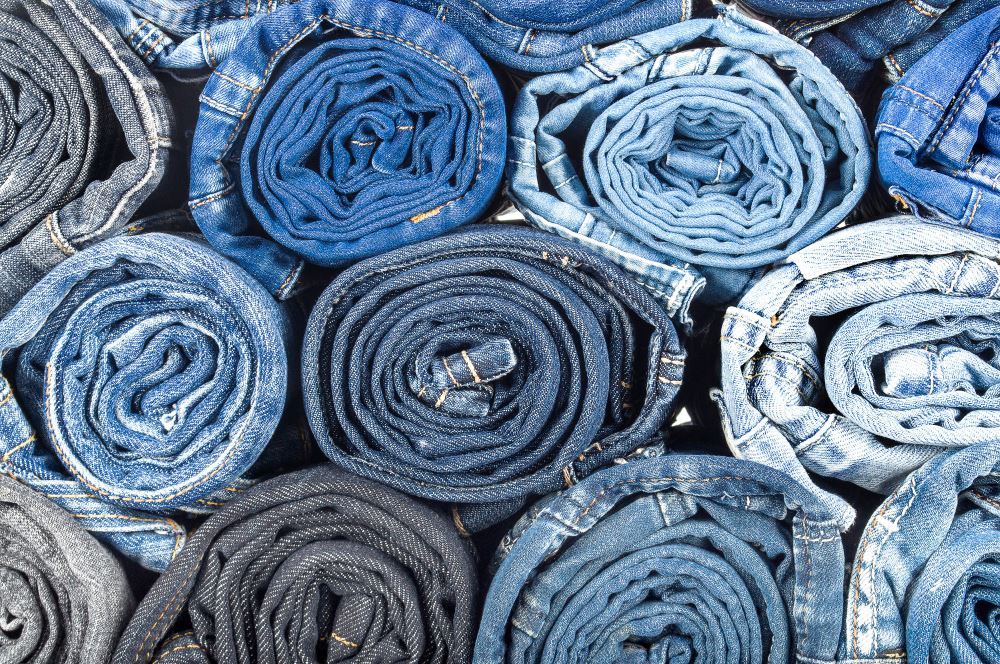
For entrepreneurs and brands looking to launch their own denim line, partnering with a reliable OEM/ODM provider is key. With low minimum order quantities and comprehensive, turnkey services, you can customize every aspect of the production process.
Quick Answer:
To have jeans manufactured, contact a trusted OEM/ODM partner like DiZNEW. They offer end-to-end services—from design and development to production and quality control—catering to both small and large orders.
Dive Deeper: Setting Up Your Production
7.1 How to Make a Jeans Factory
Establishing a jeans factory requires significant planning and investment in modern technology:
Facility Requirements: A well-planned production floor, ample storage, and dedicated quality control areas.
Equipment Investment: Essential equipment includes spinning machines, industrial looms, computerized cutting systems, advanced sewing machines, and eco-friendly finishing lines.
Workforce: Skilled technicians, designers, and quality inspectors are vital. Training programs can improve productivity and reduce errors.
Below is an example investment overview table:
Requirement | Estimated Cost Range | Key Considerations |
Production Equipment | $500K - $2M | Efficiency, scalability, modern tech |
Facility Setup | $200K - $1M | Location, space optimization, infrastructure |
Staffing & Training | $100K - $500K | Skill levels, training programs, retention |

7.2 How to Get Jeans Manufactured
If you’re not looking to build your own facility, outsourcing production is an ideal solution. A professional OEM/ODM provider offers:
Customization Options: Tailored designs and finishes, with order quantities as low as 30 pieces.
Turnkey Solutions: Handling every aspect from design to delivery.
Sustainability Practices: Use of eco-friendly materials and water-saving production methods.
7.3 The DiZNEW Advantage

At DiZNEW, we combine state-of-the-art facilities with expert craftsmanship to bring your denim ideas to life. Whether you’re an emerging brand or an established name looking to expand your product line, our comprehensive OEM/ODM services cover every step—from initial design consultations to final product delivery. With a commitment to sustainability and quality, we ensure your custom jeans meet market demands, but also set new standards in style and durability.
Conclusion
From the moment cotton is harvested to the final pair of jeans that leave the factory floor, the process of making jeans is a blend of art, science, and technology. We’ve walked you through every step—from raw material selection, weaving the fabric, precise cutting and sewing, to innovative finishing touches and rigorous quality control. Each phase is optimized for efficiency, quality, and sustainability, ensuring that every pair of jeans is not just a garment, but a masterpiece that tells a story.
If you’re inspired by the intricacies of denim manufacturing and are ready to launch or expand your denim line, why not contact us for a custom quote? DiZNEW is here to provide expert OEM/ODM services tailored to your needs. Contact us today to get started on creating high-quality, market-ready jeans that embody the perfect balance of tradition, innovation, and style.
Discover premium DiZNEW denim jeans with decorative studs for a sparkling, stylish look. Order today!
Custom washed denim jeans with vintage appeal for boutiques & designers. High-end quality, low MOQ, OEM/ODM available.
Custom raw selvedge jeans for luxury brands & boutiques. OEM/ODM, low MOQ, high-end craftsmanship.
Custom baggy cotton patchwork distressed denim jeans with raw edges and vintage wash, perfect for boutiques and luxury streetwear.